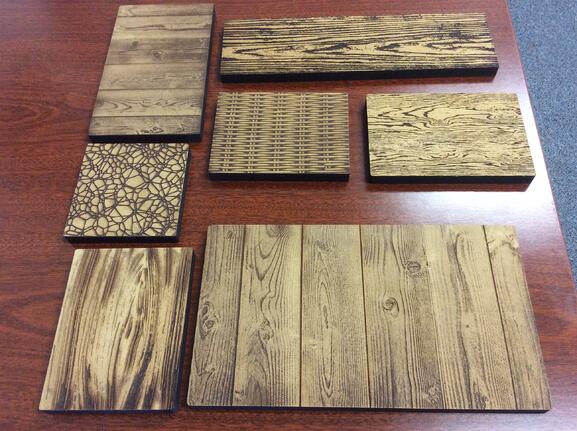

Top 5 Tips For Lasering MDF
MDF (Medium Density Fiberboard) is a strong, engineered material made of wood fibers, wax, and resin. The ability to laser cut profiles and engrave deep numbers and logos has much money-making potential in the crafting, signage, interior design, and furniture industries. Laser cutting is an easy way to process shapes with minimal scrap material. A common problem I see from customers who are trying to