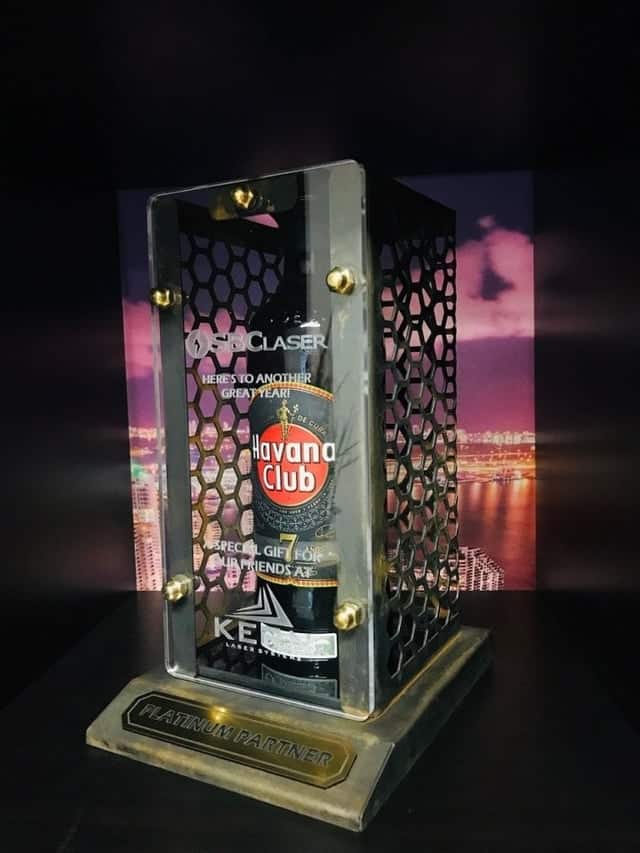

Customer Spotlight – SBC Laser
HOW TO CREATE A MIXED MEDIA GIFT USING A LASER How do you say “Thank You” to an outstanding client or customer? Nick Caito of SBC Laser demonstrates his take on adding a personalized touch to a unique gift. In this Platinum Partner build, Caito mixes steel, acrylic, and brass with a combination of laser cutting and engraving with his Kern 400W HSE laser system.