Laser Cutting System
Laser Cutter Guide
Laser cutting, a technology that revolutionizes material processing, harnesses the power of highly focused light to create a complete laser cutting machine. At the heart of this innovative technology is the laser source. Kern offers both CO2 and fiber laser options, each excelling in their respective, unique applications. The laser source works in harmony with a computer system and CNC laser motion package to deliver our core product, laser cutting equipment. Laser cutters stands out for their ability to slice through a variety of materials, ranging from delicate fabrics to robust metals, leaving behind a finish that is both clean and precise. Moreover, the versatility of laser cutting equipment makes it an indispensable asset across numerous industries, enabling intricate designs and rapid production.
Now, let’s start with the basics.
Chapter 1: What is Laser Cutting?
How laser cutting works.
The laser cutting process begins with the generation of a high-energy laser beam from a laser source. The laser beam is steered through the machine by a series of mirrors and delivered to a processing head. This head is equipped with an optic which focuses the laser beam to a small point of intense energy capable of melting or vaporizing a wide range of substrates and ultimately cut it into specific shapes, patterns, and designs.
Kern primarily offers two types of laser sources on our cutting platforms: CO2 and fiber. Both employ a different mechanism and are suited for various applications. CO2 lasers are popular for cutting wood, plastics, textiles, foam and light gauge metal. Fiber lasers, adept at cutting metals, are renowned for their speed and efficiency.
The process of laser cutting is meticulously controlled by CNC (Computer Numerical Control) software. In Kern’s case we developed our own proprietary CAD software with precision laser control, called KCAM. KCAM’s friendly user interface allows operators complete control of the laser cutting process.
What Is the Difference Between Laser Cutting and Laser Engraving?
Laser cutting and laser engraving are two distinct processes that utilize the power of lasers, but they serve different purposes and operate through different mechanisms.
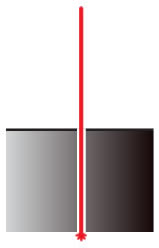
Laser Cutting
Slicing or cutting completely through a material.
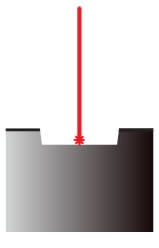
Laser Engraving
Removal of material to a given depth.
Laser cutting is primarily about precision material removal to cut or slice through materials like metal, plastic, or wood. This process involves a high-powered laser beam that moves along a designated path to cut the material all the way through, creating separate pieces or intricate designs. The focus is on the depth and completeness of the cut.
On the other hand, laser engraving is a non-contact process which uses a focused laser beam to remove material from a surface down to a specified depth. The focused laser beam delivers energy to the processing area in a manner which converts a high percentage of the light energy into heat. The primary goal of laser engraving is to leave a permanent mark that is visible and tactile, often used for labeling, personalization, or decorative purposes. Both processes are highly precise and controlled by computer systems, but while laser cutting is about penetrating and dividing materials, laser engraving is about artistic or informative surface modification.
Kiss Cutting
Kiss cutting, also known as “precision cutting” is a technique used to cut materials without penetrating the backing material, leaving it intact. This method is particularly useful for creating intricate shapes, labels, stickers, decals, gaskets, and more. Kiss cutting with a laser involves using proper software parameters to cut through the top layer of material while leaving the backing material untouched. This precise process offers numerous advantages in various industries, making it a valuable tool for many applications.
In the image shown here, the complete profile of the bird is kiss cut into the wood to give the image more definition.
Advantages of Laser Cutting
Precision and Accuracy: Laser cutting is incredibly precise and can cut materials with high accuracy, often within fractions of a millimeter. This precision makes it ideal for intricate and detailed designs, allowing for clean and sharp edges.
Versatility: Laser cutting can be used on a wide range of materials, including metals, plastics, wood, fabric, ceramics, and more. This versatility makes it suitable for diverse applications across industries such as manufacturing, automotive, aerospace, and healthcare.
Minimal Material Waste: Laser cutting produces minimal material waste because it creates narrow kerf widths, meaning that very little material is removed during the cutting process. This can result in cost savings and reduced environmental impact.
Non-Contact Cutting: Laser cutting is a non-contact process, meaning that the laser beam does not physically touch the material being cut. This eliminates the need for tool changes and reduces wear and tear on cutting equipment, leading to lower maintenance costs.
Automation and Speed: Laser cutting machines can operate at high speeds, allowing for rapid production and increased efficiency. Additionally, they can be easily integrated into automated manufacturing processes, reducing labor costs and increasing overall productivity.
Chapter 2: Laser Cutting Basics
How To Laser Cut
For those of you interested in laser cutting basics, we’re here to outline the five steps of the laser cutting process. They are:
- Ideate
- Design
- Choose settings
- Cut
- Inspect
Ideate
Deciding on a design for laser cutting can often be the most time-intensive aspect, as it sets the stage for subsequent steps. The range of possibilities for laser cutting is virtually limitless, with a plethora of compatible materials. You can work with everything from foam and plastic to wood, leather, and stainless steel. An innovative approach might involve using laser cutting to create replacements for damaged items in your home, such as crafting a new light switch plate. The following chapter will delve deeper into the various materials suitable for laser cutting.
After deciding on your laser cutting project, it’s time to unleash your creativity and envision the desired design and profile of the cut. For instance, when creating a light switch plate, you can replicate the dimensions and hole arrangement of the existing one. Spend a moment sketching on a notepad or browsing online for laser cutting inspirations. For additional ideas, refer to Chapter 6, where we’ve compiled a selection of concepts.
Design
Now that you have a good idea of what your cutting project is, it is time to create the file in a computer design software. Typically, you’re safe going with a popular design software like CorelDRAW®, AutoCAD® or anything capable of outputting a .pdf file. Other commonly used cutting file formats are:
- .dxf
- .plt
- GCODE
If your file format is in one of these listed, odds are your laser software will be compatible.
Choose Settings
All of Kern’s laser systems utilizes their proprietary KCAM laser cutting software. KCAM allows the user to easily adjust a variety of settings required for the cutting process. Within the software, you can control common parameters such as laser power, cutting speed, cut order, and cut optimization. Over the past 30 years KCAM has evolved into one of the most advanced and powerful laser cutting software on the market. Odds are, if you need to make an adjustment to the cutting outcome, KCAM will have the ability to handle the job!
Kern provides material parameters that will assist new users in determining correct settings based on your laser system setup and material being processed. Additionally, KCAM can save and load settings parameters so you can quickly move from material to material without a lot of testing of settings on scrap pieces.
For a brief run-through of what’s possible with laser cutting software, learn more about KCAM on its dedicated webpage.
It is always a good idea to give your cutting file one final look over. Look for common mistakes in your file such as duplicate or incorrect line weights.
Cut
With the settings loaded into KCAM, it is time to place the material on the cutting table, turn the vacuum system ON, press the Start command and watch the magic begin! It is always a good idea to supervise the cutting process to ensure everything works as it should. Plus, watching lasers do their thing is very entertaining. Stand back, wear your safety glasses (when using Class 4 machines) and watch your design come to life.
Inspect
Take a look at your creation! Now that cutting is complete, you can remove the material from the laser cutter and give it an inspection. How are the quality of the cuts and edges? Does your creation match what you had envisioned? If so, make sure to save your KCAM parameter for future use.
Laser Cutting Tips
1. Focused and flat.
The optic lens which the laser beam passes through focuses the beam down to a small point. In most cases the focal point should be set to the top surface of the material being cut. This ensures the smallest and most precise beam is removing material during the cutting process. Kern makes this process simple by setting the focus distance at a fixed position inside the beam delivery. A simple spacer tool is then used to set the gap between the nozzle and top surface of the material.
Generally, the best materials to cut are those with a single flat surface. However, when metal cutting a Z sensor allows the nozzle to track the metal surface with slight variations. This is an important feature of the metal cutting process as thin metal sheets will move or twist as heat is applied to them from the laser cutting process.
However, some materials are more forgiving and will not show variation in focus. Wood is a good material where you can have some variation in flatness and still get beautiful results!
2. Choose the correct air type and pressure.
The air type and pressure are a parameter that often get overlooked. Choosing an optimal air setup will ensure your cuts come out as desired. The nozzle type is another commonly overlooked aspect.
3. Take time for test cutting.
If you’re working with unfamiliar materials or lack specific settings files, it’s wise to conduct a small test cut on a scrap piece. Often, just an inch of cutting is enough to determine if the quality meets your standards. Based on this test, you can fine-tune settings like power and speed, among others, before proceeding with the final job.
Chapter 3: Laser Cutting Materials
Laser cutting is a process that works on a wide variety of materials. From laser cutting wood to metal, there are plenty of materials to work with. In this chapter, we’ve outlined a handful of the most popular materials for laser cutting and provided some advice for successful cutting.

Acrylic
As one of the most popular materials used by laser operators, acrylic is an ideal material for laser processing. One key advantage of laser cutting acrylic is its ability to produce exceptionally precise, smooth, and fire-polished cuts, ideal for detailed designs and complex shapes without the need for additional finishing.
Kern offers a wide nozzle option on their S-FOCUS optic assemblies. This wide nozzle opening allows the assist air to be dispersed over a larger area across the cut profile and will assist in achieving a flame polished cut edge quality.
Also note that different brands and types of acrylic will grant different results. An old piece of acrylic can even cut less desirable than a new piece. Make sure you know what material you are working with and make notes on the best vendors.
Mild Steel
Kern’s CO2 and fiber metal cutting machines excel at laser cutting mild steel, also known as cold rolled steel, which is a popular material in the industry. These machines utilize a high-pressure air assist that directs oxygen through the nozzle, ensuring a smooth and clean cut. For cutting thinner gauge steel, using CDA (clean, dry air) can be a cost-effective method for laser processing.
Laser cutting stands out for its flexibility and stress-free approach, often yielding high-quality parts that require little to no post-processing. The process starts by heating the metal to its melting point, which produces clean edges and eliminates dross. The lasers’ ability to create narrow kerf lines ensures precise cuts, minimizing material waste and enhancing the overall efficiency of the cutting process.
Leather
Leather cutting leather allows for intricate designs and precise cuts, creating detailed patterns and shapes with a high level of accuracy and minimal material waste. Laser cutting leather products is the perfect solution for applications, including shoes, wallets, holsters, belts and purses. The types of laser-cuttable leather are:
- Natural leather
- Suede leather
- Synthetic leather
- Vegetable Tanned leather
- Full-grain leather
- Bonded leather
Different types of leathers will have different results from cutting. As always, the quality of the material will impact laser cutting results. When working with a new leather type, always test your cutting on a piece of scrap leather to gauge processing settings.
Stainless Steel
Laser cutting stainless steel represents a cutting-edge manufacturing technique. This method is extensively utilized in diverse sectors, including automotive, aerospace, medical, and construction. The notable strengths of laser cutting, such as its capacity for crafting complex, intricate designs with remarkable accuracy, reducing material waste, and ensuring superior edge quality, render it an essential tool in modern manufacturing. This advanced technology is applied in various contexts, from producing parts for industrial machinery to crafting medical implants and devices, architectural features, and decorative artwork. Its efficiency and exactness not only enhance production processes but also foster innovation in design and engineering, setting new benchmarks in the fabrication of stainless steel components.
Textile
In the textile industry, precision and creativity are key to producing garments, complex designs, and patterns. The introduction of laser cutting has revolutionized fabric production. Offering precision and efficiency, laser technology has emerged as a popular tool for both designers and manufacturers, transforming the way textiles are crafted and designed.
Rubber
Rubber is a versatile material used in various industries, from manufacturing to automotive, healthcare, and even fashion. Its elasticity and durability make it an ideal choice for gaskets, seals, shock absorbers, and countless other applications. When it comes to shaping and cutting rubber with precision and finesse, CO2 laser cutting technology stands out as a game-changer. In this blog post, we’ll explore the benefits, applications, and the technology behind CO2 laser cutting for rubber.
Wood
Wood, like stone, is a natural material. Some woods respond to laser cutting better than others. Both hardwoods and softwoods have the ability to cut well. Wood types that respond well to laser cutting include maple, cherry, birch and MDF.
One thing operators need to look out for when choosing wood for laser cutting is glues and adhesives. When laser cutting plywood, the glue and adhesives used in its layers can cause issues such as inconsistent cutting depths and increased smoke production, affecting the precision and quality of the cut.
Other Materials For Laser Cutting
While we’ve covered some of the most popular here, there are many more materials suitable for laser cutting. We invite you to send us any materials you have that you’d like to see laser-cut. Once we receive and process them, we will ship them back to you so you can see the results for yourself. Are you interested? You can start the process here.
Chapter 4: Choosing The Right Laser Cutting Machine
Choosing the right laser can seem complicated at first until you know which variables to consider. In this chapter, we’ve included a laser cutting wattage comparison chart, along with some helpful information about laser beam power settings and processing speed. As always, if you have any additional questions about choosing the right laser, please contact us.
Laser Cutting Equipment Wattage Chart
Class II (Enclosure) | Class IV (Open Bed) | Table Size (Inches) | Available Wattages | Rotary Option Compatability | K-Vision Camera Compatibility | Metal Cutting Option Availability | |
---|---|---|---|---|---|---|---|
* Custom Sizing Available | |||||||
OptiFlex | 52×50 – 86×144* | 100W-650W | Y | Y | Y | ||
EcoFlex | 52×50 – 52×100 | 100W-250W | N | Y | N | ||
Micro | 24×24 – 48×24 | 100W – 650W | Y | Y | Y | ||
OptiDual | 52×50 – 86×144* | 100W – 200W | Y | Y | Y | ||
LaserCELL | 52×50 – 52×100 | 100W-650W | Y | Y | Y | ||
FiberCELL | 52×50 – 52X100 | 1kW – 3kW | Y | Y | Standard (Only for Metal Processing) |
Laser Cutting Wattage Comparison
Kern’s CO2 laser systems can be equipped with lasers from 100-650 watts. Wattage determines a laser’s power. Higher wattages mean a more powerful laser, and lower wattages mean a less powerful laser. There is some misconception that a higher wattage laser can be too powerful for certain applications, but it’s worth noting that high-wattage lasers can be programmed to use a smaller percentage of their power.
For instance, our 500W laser source can be dialed down to cut on even the most delicate of substrates like a thin card stock. The same 500W laser can be setup to cut through a 1” piece of acrylic with just some modifications to the KCAM laser settings.
Kern Laser Cutting Speeds
Due to high speed servo motors and linear motors, laser cutting speeds on Kern’s laser systems range from 0 inches-per-second to 20 inches-per-second. If laser cutting speed is an important factor for your machine choice, then you will want to consider our high-performance line of lasers which include the OptiFlex and FiberCELL.
Chapter 5: Accessories & Supplies
Laser Cutting Machine Accessories
Laser system accessories and attachments help owners and operators expand their capabilities and improve their output. Below, we’re describing some of the most popular system attachments and options: k-vision camera registration, pipe rotary and metal cutting.
K-Vision Camera Registration
The k-vision package is a fully integrated hardware and software solution that allows for accurate cutting of preprinted materials. This process starts with a nozzle-mounted camera which automatically measures the dimensions between registration marks on printed materials.
The system then uses these measurements and the registration marks of the original cutting file to compensate for distortion and rotation. The slight adjustments that k-vision makes to the cutting file results in a perfectly matched cutout in the material being processed. The entire camera system can be easily removed and stored in a protective box when not in use.
Wheel And Pipe Rotary
A z-axis rotary attachment outfits a laser system with the capability to process pipes, rods and other cylindrical items. Without a rotary attachment, laser engraving can only be done on relatively flat surfaces, but with the attachment, an entire world of possibilities opens up.
A laser system with a rotary attachment is able to engrave objects like walking sticks, canes, liquor bottles, and flashlights.
Metal Cutting
The metal cutting laser option makes it possible for CO2 lasers to cut a whole host of metals. You might ask why is the metal cutting system beneficial for laser marking? The metal cutting option includes a height following system which allows the laser beam to stay in focus over the entire metal sheet. When considering focus, metal is much less forgiving than materials like wood and plastic. The height follower can be used when engraving to allow for full table marking of aluminum, mild steel, and stainless steel.
This metal cutting option was developed internally by the team at Kern Laser Systems, and it is compatible with four out of five CO2 lasers in the Kern lineup. They are:
With any of these options—vision cameras, pipe rotary, or metal cutting—operators can outfit their laser system with the engraving capabilities to take on complex projects.
Chapter 6: Laser Cutting Applications
Do you have some laser cutting project ideas in mind? When it comes to laser cutting projects, you’re truly only limited by your own imagination. For those of you looking for laser cutter project ideas, we’ve provided some examples from our very own customers. Each laser-cut item you’ll see in the next section was processed on a Kern laser system. We hope this next section leaves you feeling inspired and full of ideas for your next project.
Plaques & Awards
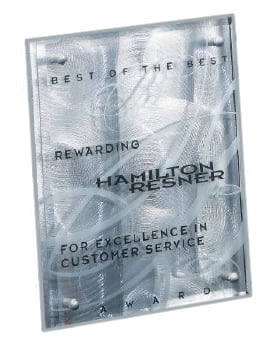
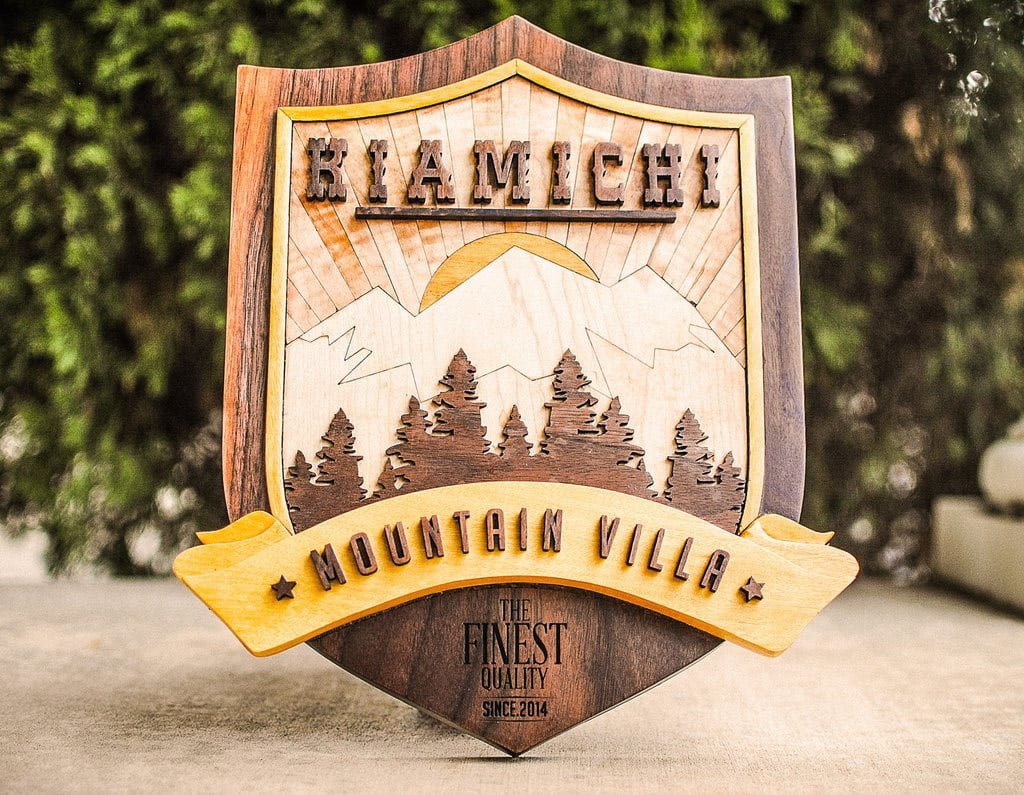
Signage

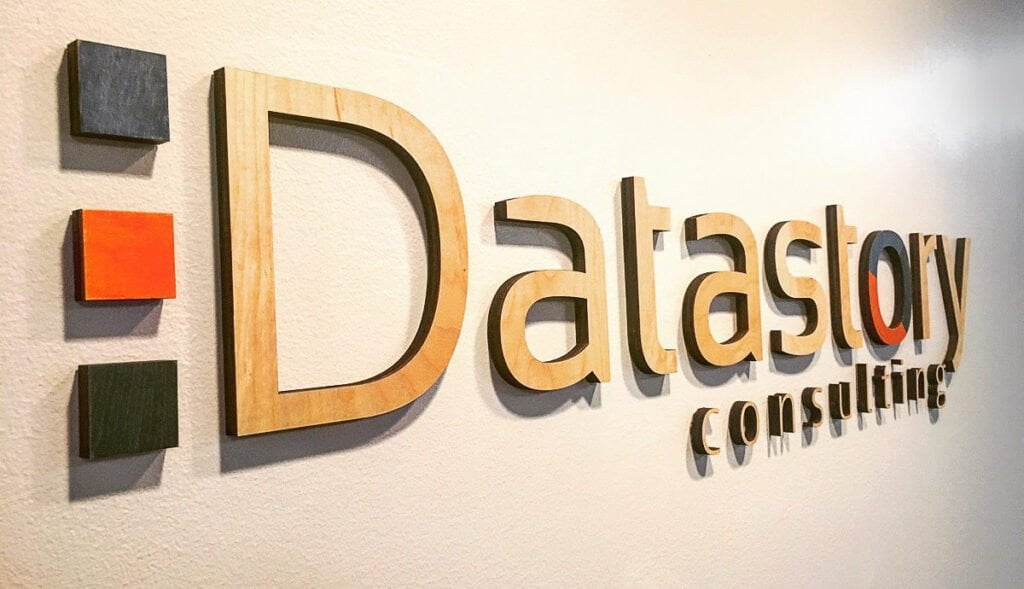
Foam Tool Cutouts
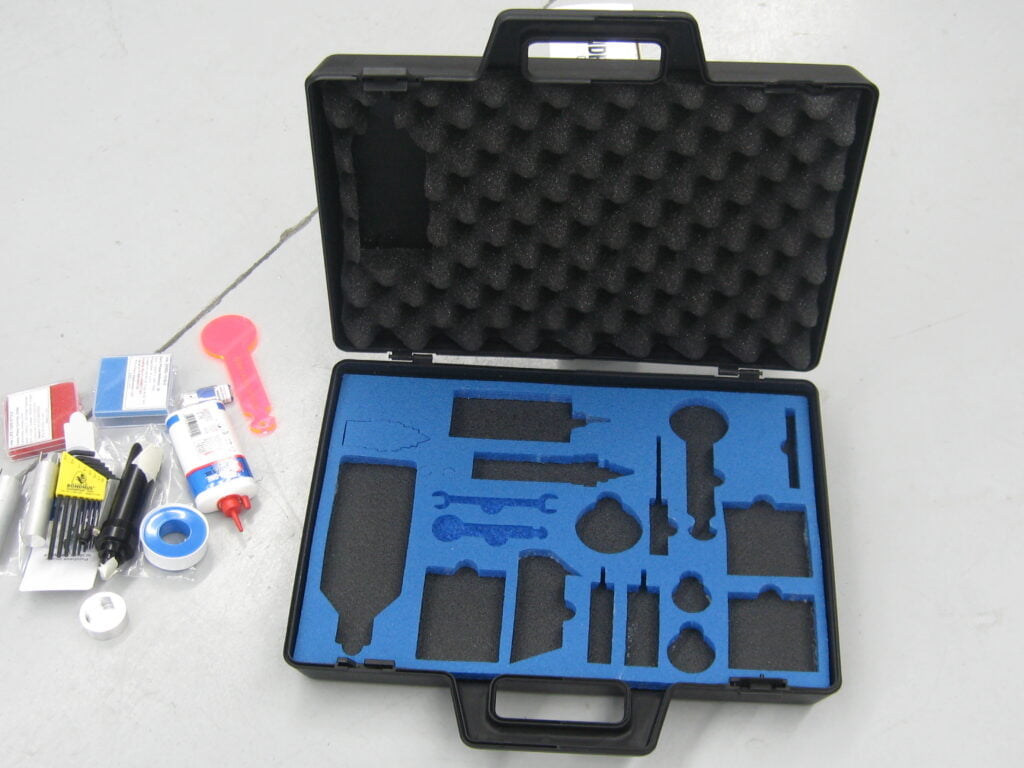
Kitchen Platters & Cutting Boards
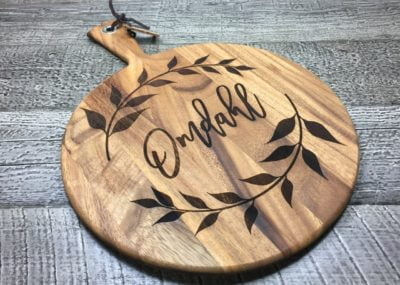
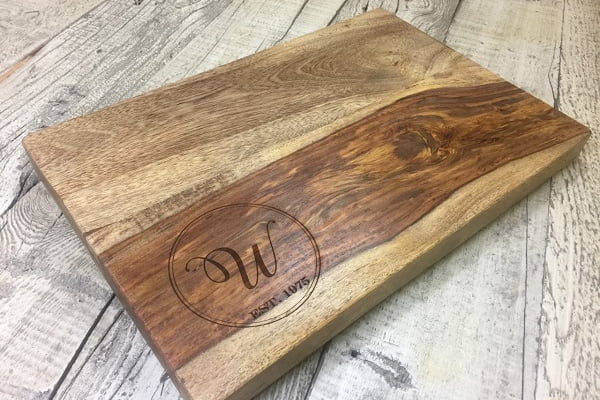
Chemetal Laser Cut
Musical Instruments
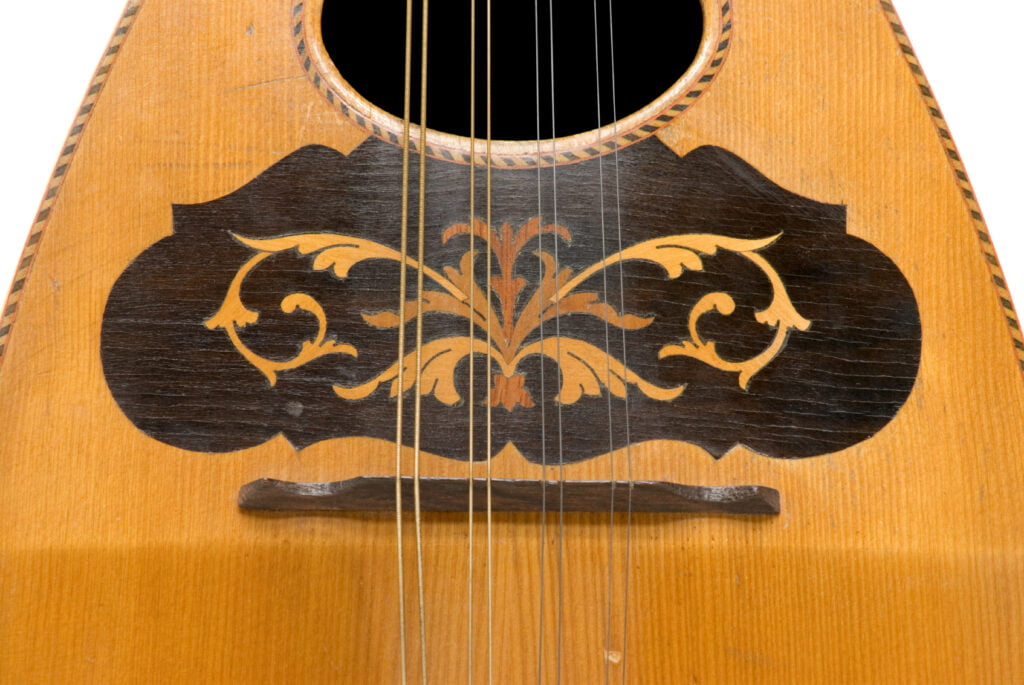
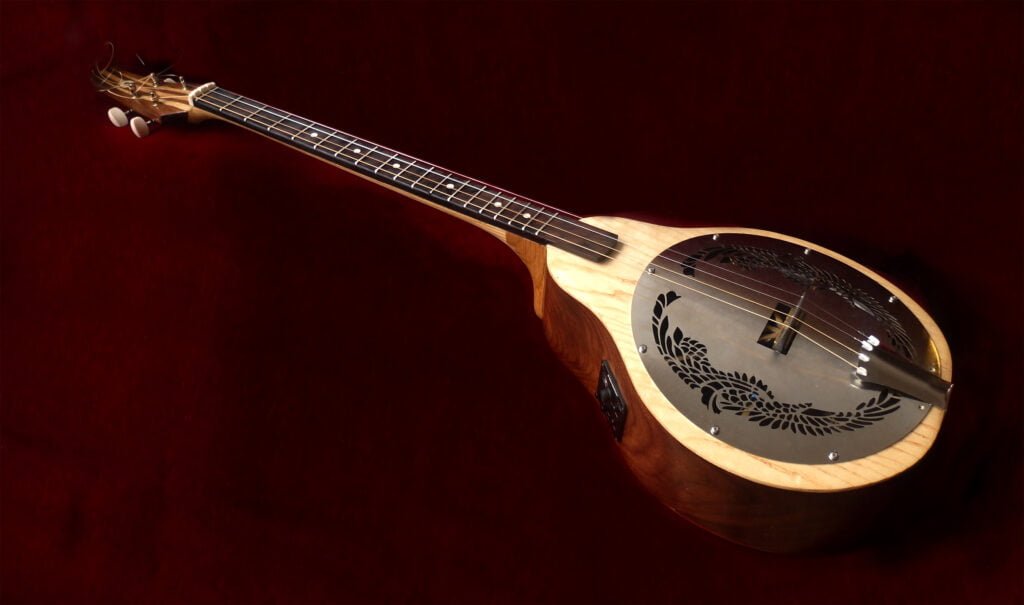
Scale Models
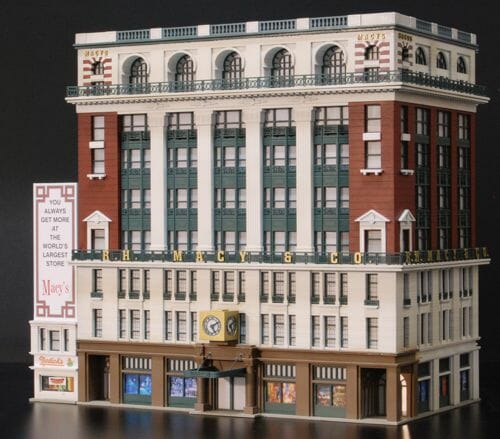
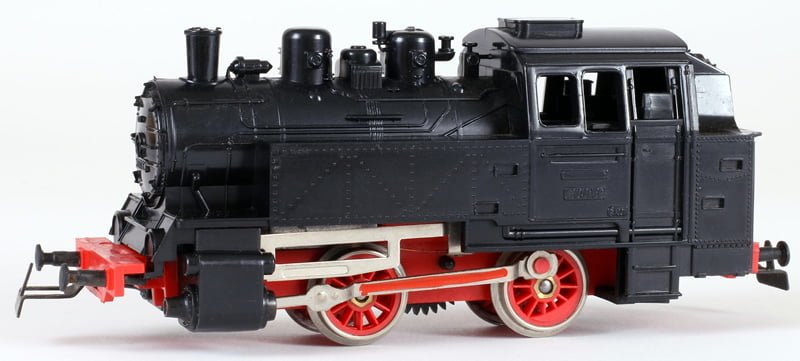
Tap Handles
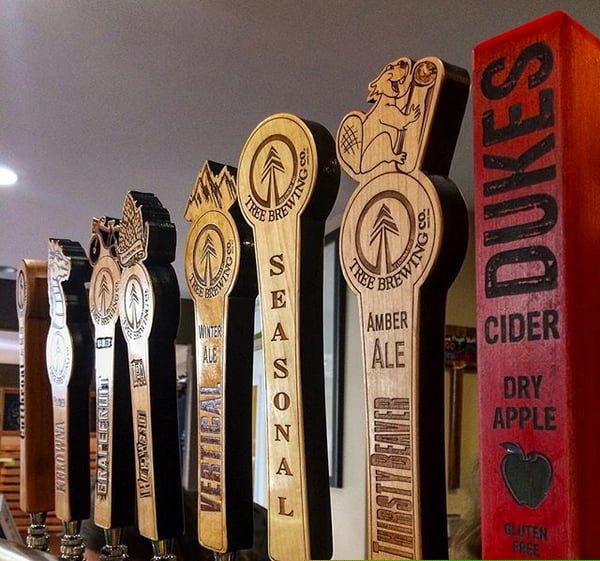
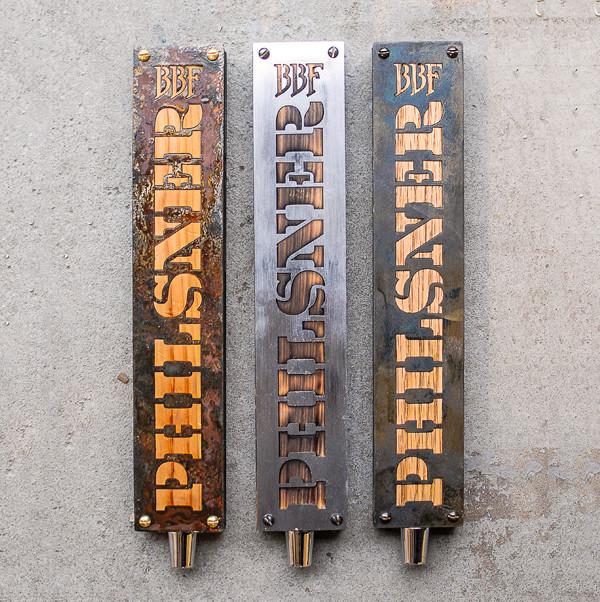
Nameplates, Tags and Labels


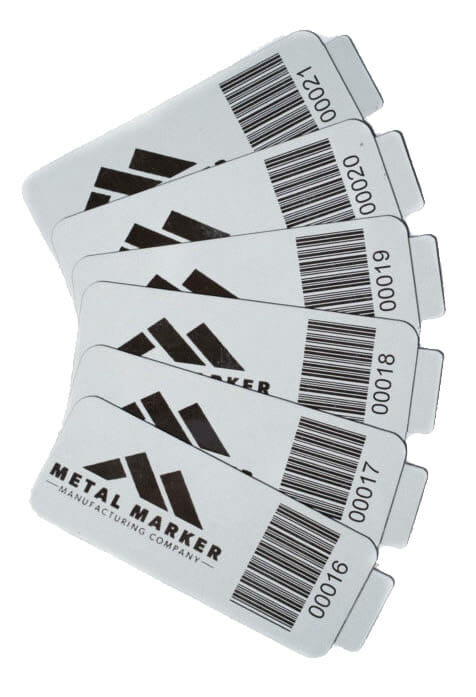
Learn More About Laser Cutting
While we’ve covered a whole lot about laser cutting here, there is so much more to know. If you have any questions, whether they are application-specific or not, please do not hesitate to contact the friendly, knowledgeable staff here at Kern Laser Systems. You can contact us here or request a samples kit! We’d love to hear from you.
Thank you for reading, and we hope you have a great day!