Coated Metals
Lasers have proven to be particularly efficient and precise technology for processing coated metals. You can etch many different types of coated metals using the modern laser machines from Kern and, in doing so, benefit from a wide range of possible applications. High throughput speeds, precise contour accuracy and consistent quality standards – whether you’re manufacturing prototypes or small or large numbers of copies – are just some of the benefits of modern laser technology.
Anodizing is a process used to promote the formation of a protective oxide layer on the surface of a metal. As long as it remains fully intact, it protects the metal from corrosion. While several non-ferrous metals can be anodized, aluminum responds most effectively to this process.The process is also used to give the aluminum a wide variety of colors.
Powder coating, as its name implies, involves coating an object with a powder-based substance. It is an electrostatic process, whereby the coating particles are electrically charged with a polarity that is opposite to the part to be coated. The difference in charge causes the powdered particles to adhere to the metal’s surface. The coated object is then heat-treated in an oven to harden the coating.
Painting is a popular choice for mild steel outdoors signage. Steel will quickly rust in the outdoor elements and a simple spray or brushed-on paint adds a cheap and simple layer of protection.
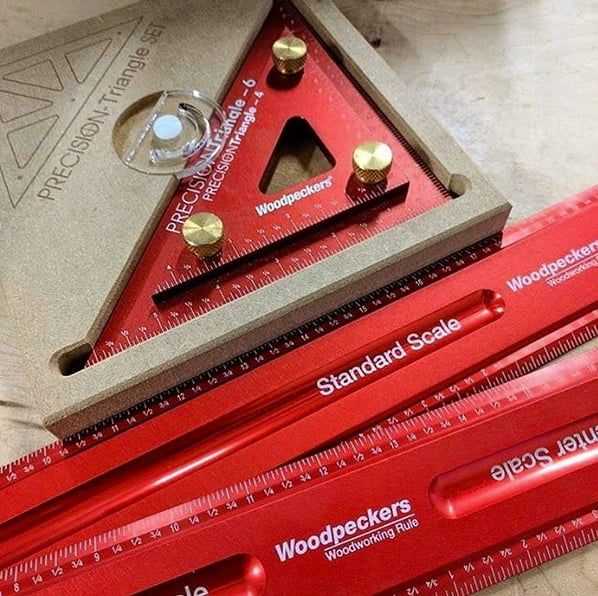
